POCKETING
There is the new chance to split the roughing in Z in more portions. The aim of this modification is to preserve the tool from breaking and overheating.
It has been noticed that during the roughing of the first side, the tool tends to rapidly turn and go down in cavities, occasionally very small, as sometimes happens to the space between two connectors. In these cases the material (e.g.: Zirconium) which is not removed could "block" the tool, impeding the cooling and stressing it too much with the risk to break it, especially on high speed machines.
To avoid this problem it is now possible to split the roughing of the same side in "phases" and to perform the roughing on the opposite side between these "phases". The aim is to make an hole in the disk and consent to get back on the previous side to go on with the machining avoiding a dangerous overstock of the material removed.
To set the "phase" is necessary to input the code <PORTIONn/m>, in the name of the machining, where 'n' sets the number of the phase and 'm' sets the number of total phases.
For instance: <PORTION1/2> or <PORTION2/2>
Example of machining sequence:
- roughing of the cavities side with <PORTION1/2>
- roughing of the opposite side, without codes "<PORTION...>"
- roughing of the part still to be machined of the cavities’ side, with <PORTION2/2>
- other machinings
Otherwise:
- roughing of the first portion of the cavities side with <PORTION1/2>
- eventual elimination of the stock interference with the axes of the cavity, to set free the access to the cavities with strong inclination
- roughing of the cavities
- finishing of the borders
- finishing of the cavities
- roughing of the opposite side, without codes "<PORTION...>"
- roughing of the part still to be machined of the cavities’ side, with <PORTION2/2>
- finishing of both sides
Attention:
This kind of managing is still a work in progress and could be refined and improved in the calculation times and in the length of the machining tool-paths. Your tests will be very useful for future improvement.
The safety of the tool-path has been tested and did not show any variation in the behaviour.
NEW FINISHING METHODS
In the 3d curves pocketing machining like "<SPIRAL>" it is now possible to set more than one "zone" in the same machining.
For instance it is possible to input, inside the machining's name, the words:
<SPIRAL0/5/0.05>
<SPIRAL5/0/0.15>
to set which kind of machining to execute: with 0.05 mm increment for the first 5 millimetres of the cavity, starting from the "prep-line", and with 0.15mm increment for the rest of the cavity.
The parameters of the "<SPIRAL...>" strategy are 3: start, end and increment.
The start and the end can be negative, in this case the machining will begin from the back instead of the border.
![]() |
In this picture we set 0.05 for the first 3 mm and 0.2 from 3mm to the end of the cap. Also this Strategy can be downoaded from the website. |
STRATEGIES TO DOWNLOAD
ZIRCONIUM |
|
LAST UPDATE 09/06/2010
Strategy for the zirconium machining of a bridge featuring 2 or more non parallel insertion's axes. |
|
LAST UPDATE 21/06/2010
Strategy for the zirconium machining of a bridge or single caps featuring internal and external undercuts, re-machined with a Lollipop tool without using 5 axes. |
DETECTION OF SINGLE AXES IN BRIDGES
In the SUM3D Dental update currently available, it has been added the automatic detection of insertion axes during the STL import.
By activating the option "undercut's optimization"
during the import it is calculated the medium axis of the bridge (as published some weeks ago), and now are calculated the insertion axes of each bore of the bridge too. Also the strategies’ management has been modified to allow the roughing and finishing of each cavity and its own axis, removing the undercut during the roughing phase.
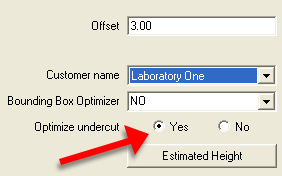
SINO-DENTAL 2012
AMICI DI BRUGG 2012
EUROSTAMPI 2012
IDS 2011
COLLOQUIUM 2010
Expo 2009
Articles:
- CHIP BREAKERS CYCLE
- SUM3D Dental works this way.
- Training in the UK
- Workshop: the dental item from scan to milling
- 5 AXIS IN CONTINUOUS
- Change of address!
- LITHIUM DISILICATE AND CERAMICS
- CHANGES IN THE “PORTION” CODE
- We wish you health, happiness and success for the New Year!
- SINTERING STABILIZER
- 5 AXIS CONTINUOUSLY
- DIMENSIONAL CHECK
- 4 AXIS IMPLANTS’ MILLING
- POCKETING
- NEW FINISHING METHODS
- STRATEGIES TO DOWNLOAD
- UNDERCUTS’ OPTIMIZATION
- AMICI DI BRUGG – Rimini, May 27th – 29th, 2010
- TIME’S CALCULATION
- SUM3D DENTAL AT EXPODENTAL MADRID
- EXAMPLE OF IMPLANT’S MACHINING By ESTUDIO PREVIO MADRID
- A NEW SUM3D DENTAL INSTALLATION ON HERMLE
- CREATE RAW
- USING SUM3D DENTAL WITH DATRON
- SUM3D DENTAL VIDEOS
- SUM3D DENTAL
- DENTAL SHAPER
- SUM3D DENTAL STATISTICS